Products
What Happened In Minutes Could Set Off A Chain of Delays
Mid-Atlantic and East Coast homebuilders brace for building materials supply disruptions and cost increases after this week's tragic bridge collapse, shutting down the Port of Baltimore.
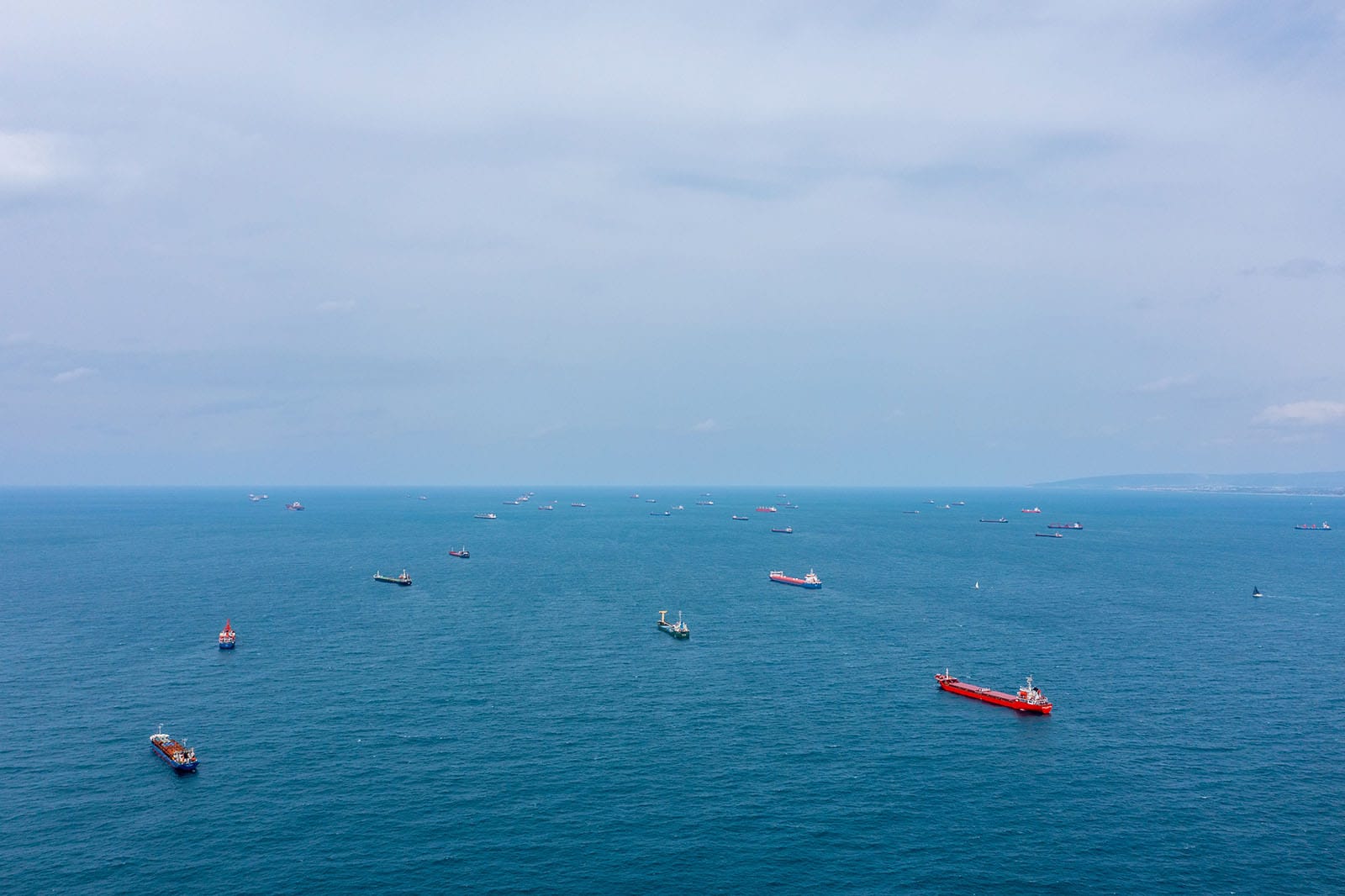
He was always so full of joy, and brought so much humor to our family."
Carlos Suazo, brother of one of the six construction workers who went missing and is presumed to have died early Tuesday as the Francis Scott Key Bridge in Baltimore collapsed, provided a statement to the New York Times. Carlos Suazo's remarks about Maynor Yasir Suazo Sandoval – a 30-something year-old immigrant from Honduras 17 years ago – noted that he had a "special talent for repairing and operating all kinds of machinery, and said that he dreamed of operating his own business."
The death of Maynor Yasir Suazo Sandoval and the loss of five other lives, reported to be those of construction contractors doing overnight maintenance on the bridge, is, no doubt, the most grievous of the outcomes of the overnight catastrophe this week in Baltimore Harbor. Construction workers – residential, industrial, commercial, institutional, you name it – are more than likely to be men like Maynor Yasir Suazo Sandoval, who would have celebrated a birthday with his young family on April 27.
All but one of the eight men [two of whom survived the bridge's collapse] worked for Brawner Builders, a contractor based in Baltimore County, the company said. The men who went missing after the collapse were all immigrants from El Salvador, Guatemala, Honduras and Mexico, according to consular authorities and the nonprofit," the Times reported.
As much as we may already be doing, we need to do more for the safety, production, regard, and value of our construction front line workers. Night and day. They are the names, faces, families, and communities of construction capability in the U.S.
Heather Cox Richardson writes:
Around 39% of the workforce in the construction industry around Baltimore and Washington, D.C., about 130,000 people, are immigrants, Scott Dance and María Luisa Paúl reported in the Washington Post yesterday.
Some of the men were undocumented, and all of them were family men who sent money back to their home countries, as well. From Honduras, the nephew of one of the men killed told the Associated Press,
The kind of work he did is what people born in the U.S. won’t do. People like him travel there with a dream. They don’t want to break anything or take anything.”
Analysis from the Times and other news sources took stock the next morning, all of them concluding that the tragic accident would set off a paroxysm of effects on supply chains, given that Baltimore ranks as the 17th busiest port and logistics center by cargo tonnage in the U.S.
Baltimore isn’t a huge port for containers — about 3% of the total on the East and Gulf Coasts — but it handles the nation’s largest volume of automobiles, as well as a lot less-consumer-facing items like coal, gypsum and lumber. With total trade last year amounting to about $80 billion, every day Baltimore is closed is another $217 million that’s not crossing its docks." – Bloomberg
As of yesterday, there's no definite estimate as to when to expect the port to reopen.
Vessel traffic at the Port of Baltimore was completely shut down immediately after a containership hit the Francis Scott Key bridge just south of port early Tuesday. Maryland Gov. Wes Moore said there was no estimate of when the fifth-busiest container port on the U.S. East Coast would reopen." – Wall Street Journal
Occurring when it did, Tuesday's tragedy sent post-traumatic-stress shockwaves out among homebuilders – particularly mid-Atlantic and East Coast-based operators – signaling that important days and weeks of hard-won gains in their construction cycles may be at risk.
A bulletin from the National Association of Home Builders notes:
Top imports related to the home building industry include:
- Plywood, veneered panels and similar laminated wood ($425.07 million), which represents 16% of the U.S. total import value for 2023, making it the most important port for plywood imports.
- Gypsum ($23.99 million), representing 14% of the U.S. total import value for 2023 and the highest level of gypsum imports for any U.S. port.
- Sawn lumber ($198.22 million), which represents 3% of the U.S. total import value for 2023, making Baltimore the 11th most important port for sawn lumber imports.
Other items of note include electrical transformers ($263.74 million), which represents less than 1% of the U.S. total import value.
Homebuilders, eager to capitalize on a thus-far strong Spring Selling season, braced for potential disruptions in the supply of essential building materials. This could delay the start and progress of new home constructions. Disruptions may result in delayed completions and closings, adversely affecting builders' balance sheets, and complicating loan repayment schedules. Builders are now challenged to navigate these uncertainties to maintain project timelines amidst strong market demand.
From Pennsylvania through the Carolinas and into Georgia, word is out among operators to be prepared for materials and supplies disruptions.
The closing of the Baltimore Port could have some major impacts on building materials, specifically sheetrock," one operator writes to his team members. "One of my friends from Baltimore shared with me this morning that the Baltimore Port is the largest shipping location for sheetrock on the East Coast. I am sure the industry is finding other places to bring those supplies but wanted to at least put it on your radar so that you can be prepared if there is going to be a shortage."
What's more, this week's calamity is only the latest in a series of events, developments, and evolving trends illustrating fragility in global supply chains, not to mention the ecosystem of building and construction supply and distribution channels.
The problem is that supply chains have been under stress from multiple directions lately.
Houthi attacks on ships in the Red Sea and Panama Canal bottlenecks have lengthened delivery times and increased costs for companies that rely on East Coast ports.
The pause in maritime traffic at the Port of Baltimore adds one more point of pressure for trade in the region. This may lead more shippers that have a choice to send more freight through West Coast ports, which have not suffered much from the Red Sea attacks and Panama problems." – The Conversation
Going back to Covid in 2020, the vulnerability of supply chain systems, with huge knock-on impacts to an already stressed housing supply and demand dynamic has come clearer as a business risk.
If there’s one lesson we learned about the supply chain in recent years, it’s that sudden increases in container volumes arriving in U.S. ports can compound into congestion and delays. This was most evident during the peak of the pandemic-induced supply chain crisis, when over 100 ships were waiting off the coast to unload at U.S. ports.
We don’t yet know what caused the power loss that led to the crash in Baltimore or what could be done to avoid tragedies like this in the future. As we mourn the loss of life, what’s obvious to those of us in the shipping industry is that chronic underinvestment in America’s ports makes them ill-suited to handle the surging volumes they are likely to experience, as traffic planned for Baltimore is shifted to neighboring ports." – Ryan Petersen, CEO, Flexport, New York Times
Our friend and advisor, Kenzai founder and author Ken Pinto tells us:
Images of that huge container ship and that extraordinary image of the collapse bridge in Baltimore carry across what this should mean to homebuilding and building materials supply business leaders: Supply chains are more fragile than they continue to think they are. Have the lessons-learned of Covid and the breakdown of supply chains kicked in? Not much. We have the potential for the same breakdown to happen all over again because of how little has been done to mitigate what could and does happen."
MORE IN Products
T-Time Ticking? Ken Pinto's Q4 Homebuilding Commodities Report
With end-of-year price hikes looming, homebuilders are pushing back harder than ever on material costs. Sharpened cost-control strategies, from commodity tracking to supplier negotiations, will be critical as builders brace for supply chain and demand-driven price shifts.
Brace for Impact: Builders Must Expect 2025 Supply Shocks ... Again
Strategic sourcing and supply chain sage Ken Pinto reveals how tariffs, labor policies, and thin margins could test builders’ resilience in a turbulent 2025. "Covid supply shocks were a missed opportunity."
Margin Pressure Gauge: Ken Pinto’s Q3 LBM Commodities Report
Moving from lump-sum contracts to unit pricing to find ways to reduce costs in the supply chain can be a win for homebuilders worried about high construction expenses.