Products
Tire Tracks: How Builders Can Save On Last-Mile Costs, ... And Ease Supply Chain Stress
Think the last-mile shortage of truckers is an external factor builders have no sway to impact or solve? Think again. Here, TBD Dream Teamer Ken Pinto proposes a way to gain last-mile capacity by the truckload.
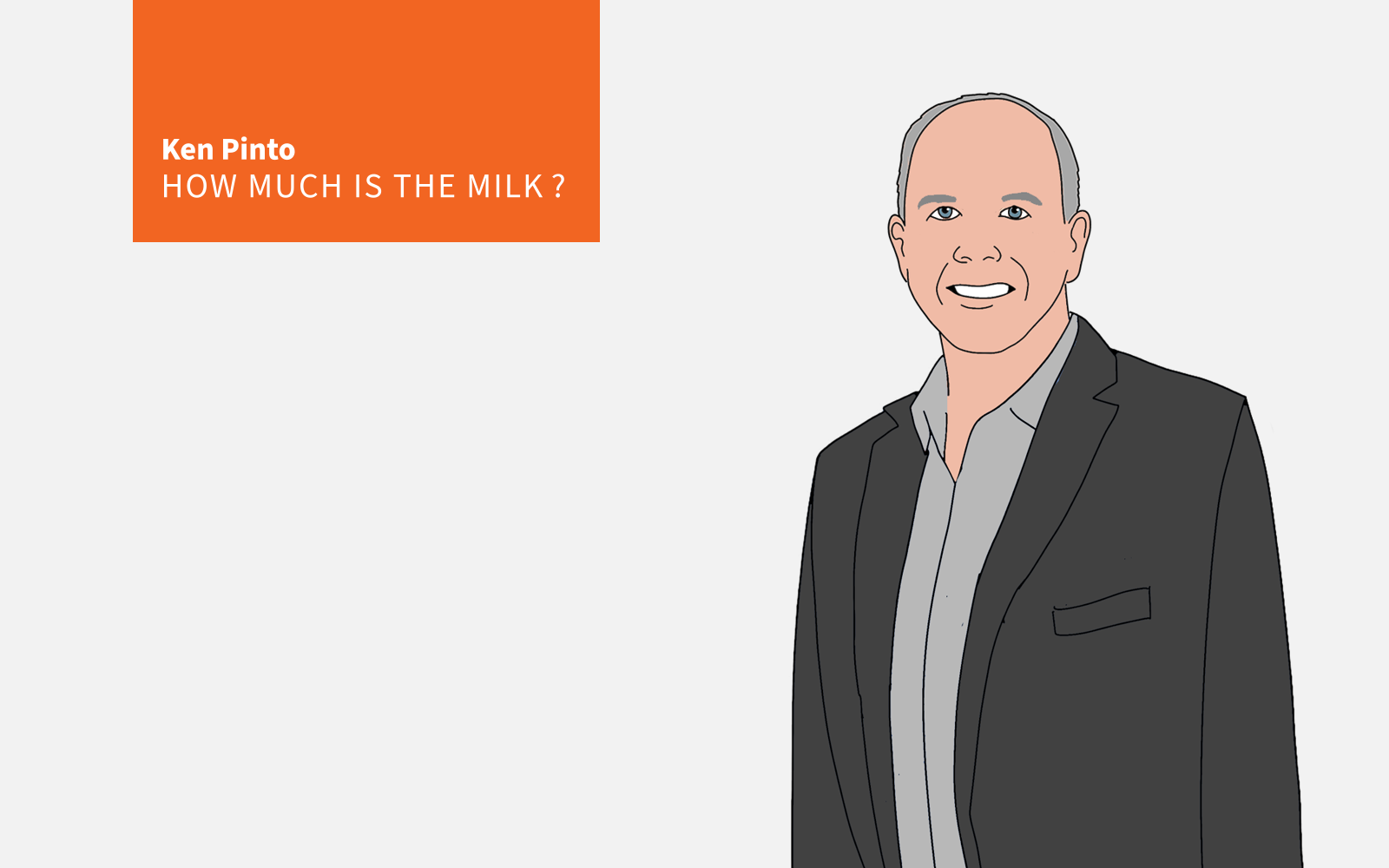
[Editor's Note: Here's the 4th installment in our Master Class series on supply chain, strategic sourcing, purchasing, and procurement solutions from TBD Dream Team member, Ken Pinto. Ken's just published, How Much Is The Milk?, now available directly, and through Walmart, and Anderson's Bookshops, details time-tested tactics, learnings, and strategies that connect builders' needs to discover better processes with improved outcomes for their manufacturer and distributor channel partners. At a time – the pandemic era – that has profoundly shocked supply chain resiliency, Ken's carefully designed analysis is a blueprint for future fit value chains.]
The News
When we consolidate distribution, and fewer trucks come to the job site, we are effectively adding production capacity to an already strained part of the supply chain; trucks and truck drivers. Imagine if all builders reduced the number of trucks coming to their job sites by 20%. The additional trucking capacity would put a dent in our supply chain woes." – Ken Pinto
The Backstory
A team member, some years ago, suggested we put light fixtures and door hardware on the same truck to the jobsite. The idea was to save last-mile trucking costs. I shrugged it off.
These products come from different manufacturers and different channel distributors, after all, and the odds of pulling off the new logistics were tiny. Still, the idea gnawed at me. Out of curiosity, I sat down and did the math. What if we could get past the logistics hurdles. How might it work? As absurd as the idea initially sounded, it grew on me. Beyond lighting and doorknobs, how many more products could I combine to save more money? After all, every bit counts.
Back-of-a-napkin arithmetic made things clearer. Each delivery to a job site cost – at the time -- about $300. There are about 35 deliveries for each house. It added up to last-mile delivery costs of $10,500 per new home.
I wondered if I could affect a 20% decrease and net about $2,100 in savings. Worth trying? I thought so.
The simple solution of putting door hardware and light fixtures on the same truck doesn't reflect game-changing genius. It's more like common sense. Why, then, haven’t we been doing it all along?
In cases where homebuilders use turn-key subcontractors to provide and install one category of building materials, the likelihood of 35 separate subcontractors all teaming up together to combine products on delivery trucks was slim.
Typically, for example, a single distributor sells drywall and stucco materials. However, the subcontractors for drywall and stucco hired by most homebuilding operations tend to be different entities, each with distinct operational challenges to solve. The same distributor ends up selling products to two of your subcontractors.
The solution
Consolidating distribution – whether from multiple distributors or multiple manufacturers – requires a whole-house perspective. Once you step back and map all the deliveries to a house as a whole, items like door hardware and light fixture consolidation in the last-mile makes the most sense, as normally, these two products need to show up at each new home on the same day.
When subcontractors operate as silos, they seldom discover this solution.
Few builders – NVR being an exception to the rule -- account for specific strategies to reduce logistics costs. Those who do win an advantage.
We took a leap of faith and combined a few products to find out what kind of savings we could find.
On door hardware and light fixtures, we netted about $135 in savings. Floor tile and drywall, about $85. Stucco and drywall, when combined, dropped $1,300 to the bottom line (including a private label deal).
We had our evidence!
Why didn’t we do this a long time ago? The folks managing material deliveries had the wrong perspective; one trade category versus the whole house.
When we reduce the number of trucks needed to deliver materials to our job site, we reduce materials costs. Look for opportunities to reduce the number of tire tracks on your jobs and watch the savings add up.
Join the conversation
MORE IN Products
T-Time Ticking? Ken Pinto's Q4 Homebuilding Commodities Report
With end-of-year price hikes looming, homebuilders are pushing back harder than ever on material costs. Sharpened cost-control strategies, from commodity tracking to supplier negotiations, will be critical as builders brace for supply chain and demand-driven price shifts.
Brace for Impact: Builders Must Expect 2025 Supply Shocks ... Again
Strategic sourcing and supply chain sage Ken Pinto reveals how tariffs, labor policies, and thin margins could test builders’ resilience in a turbulent 2025. "Covid supply shocks were a missed opportunity."
Margin Pressure Gauge: Ken Pinto’s Q3 LBM Commodities Report
Moving from lump-sum contracts to unit pricing to find ways to reduce costs in the supply chain can be a win for homebuilders worried about high construction expenses.