Products
Lumber Liquidated: What's Next For The Commodity That Ate Building?
As lumber and engineered wood product prices break all historical price barriers, producers begin to pump capital into mill capacity expansion. Too little too late?
The picture may be worth a thousand words, but at a cost of tens of millions of dollars for builders and their homebuying and remodeling customers.
Here's the picture (and the background story from Visual Capitalist):
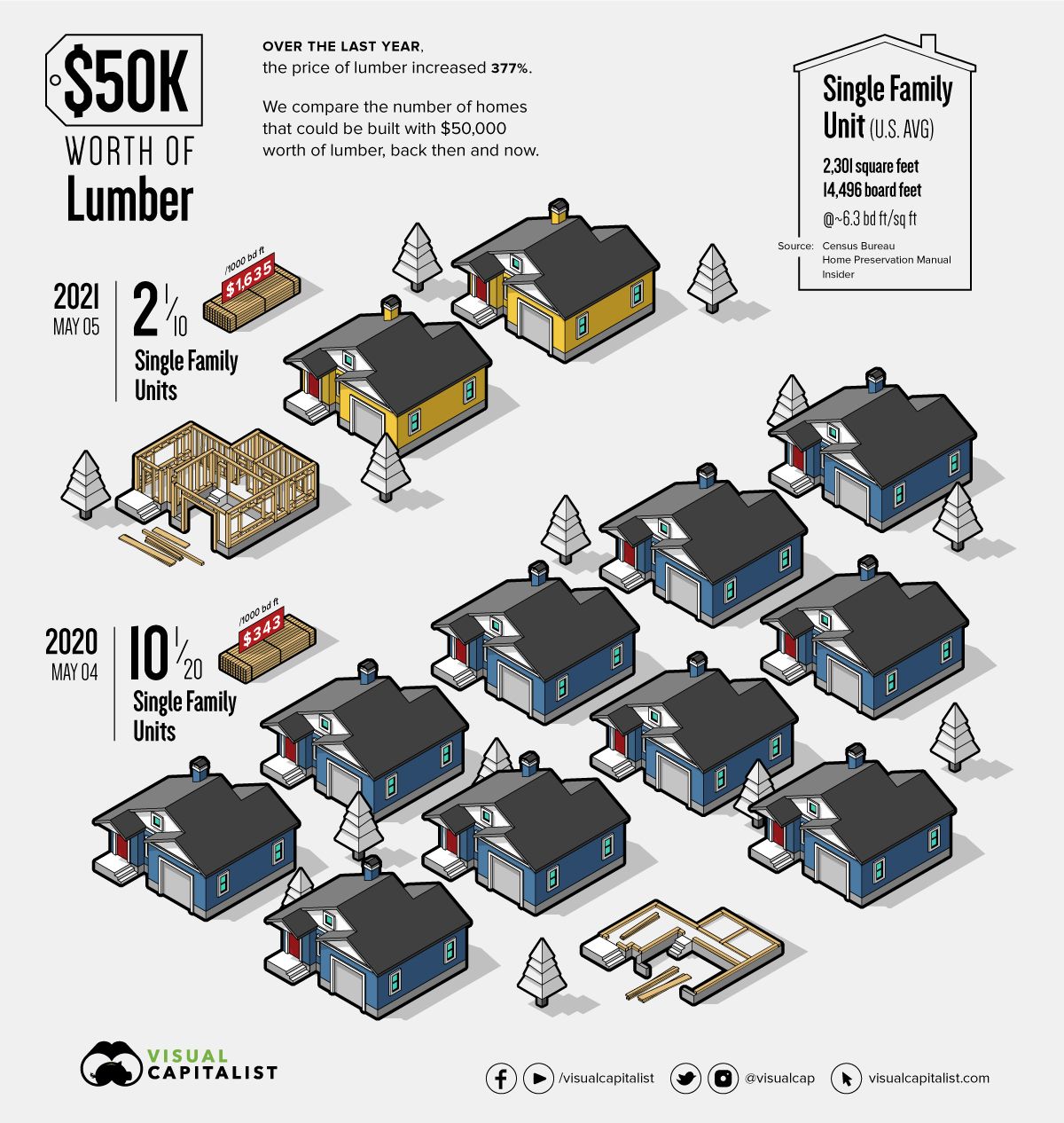
Here now are the 1,650 or so best-written words that bring readers into the cross-hairs of builders' lumber and wood products crisis, from Slate's Henry Grabar.
The picture's worth the words.
But the story – which explores the multitude of factors that have rivered as converging forces of shorter supply and extra robust demand into the moment's grand painful predicament for producers of wood-based structures – reveals the blackbox crux of the logjam.
Robbins Lumber has a solution, but it wasn’t cheap. Two years ago, the family committed $30 million to an on-site biomass power plant that uses the mill’s waste chips to generate power for thousands of local homes—and enough heat to dry its own white pine boards in a massive kiln building before they are shipped to market. The expense of that project is part of the answer to the question: Why not build another sawmill?
The other lies inside the mill. Step inside and see the bewildering array of technology that’s required to turn a log into lumber. A metal detector, for one thing: Maine’s eastern white pines may be a century old by the time they are felled to make boards, so a tree might contain hooks, nails, or bullets that can gum up the works. More expensive are the computer scanners that make instantaneous decisions about how to slice a plank into marketable boards for maximum value, based on the location of cracks, knots, and other imperfections; the calculations and the cut are made in a fraction of a second. There are 30-pound saws that shape the planks.
Residential construction's cyclical nature – booms followed by busts followed by cheap access to resources that fuel the next boom – have been the building ecosystem's ethos of rules, models, and behaviors.
Cyclical rigidities – where the same things happen over and over again with different timing, duration, and trajectories – have been innovation and modernization inhibitors on a massive scale.
Now, at tulip-mania inflationary costs that have added $35,000 to what people now have to pay in Average Selling Prices for new homes, and $119 per month added to per-door rents – effectively lopping 5.5 million would be new home buyers from the prospect universe – the toll of this visualization is nearly incalculable.
Now – do you believe it? – North America's leading lumber producers are "planning to ramp up production" with programs to expand capacity at their facilities.
American Journal of Transportation staffers Mary Nicholson and Daniela Sirtori-Cortina write:
The expansions will be primarily in the southern U.S., where there is an abundance of planted timber available to be harvested. They should help to increase overall inventories in the country and push prices off their record highs over time. But that won’t come fast enough to alleviate supply constraints during the peak building season.
“We remain optimistic about the favorable market fundamentals we’re currently seeing supported by the underlying environmental benefits of building with wood, which have never been more clear and more widely accepted,” said West Fraser Chief Executive Raymond Ferris, speaking to analysts Friday.
Though 80% of the Vancouver-based company’s operations are now outside of British Columbia, which has historically provided significant amounts of spruce-pine-fir wood that is preferred by many home builders, Ferris noted the log costs in the province are rising.
West Fraser plans to invest roughly $150 million at five of its U.S. South lumber mills under its strategic capital program. Already, it’s increasing the number of working shifts at mills where possible, the company said.
“These investments will increase our capacity and increase the value of our products while reducing production costs overall,” Ferris told analysts.
The risk, of course being that investment commitments at this "inning" of a cycle whose genesis traces back to grinding recovery from The Great Recession, could prove to self-fulfill prophecies that big upgrades and retooling can languish at great cost and financial ruination when the tide of demand reverses.
Still, as the Chinese proverb notes in answer to the question, "when is the best time to plant a tree?" Forty years ago.
And the second best time? Today.