Technology
A Homebuilding Breakthrough That Cracks The Code...Literally
Most prefab systems clash with existing homebuilding models. Fornidos integrates seamlessly — faster, cheaper, financeable, and, .... newsflash: Pre-approved for local building codes.
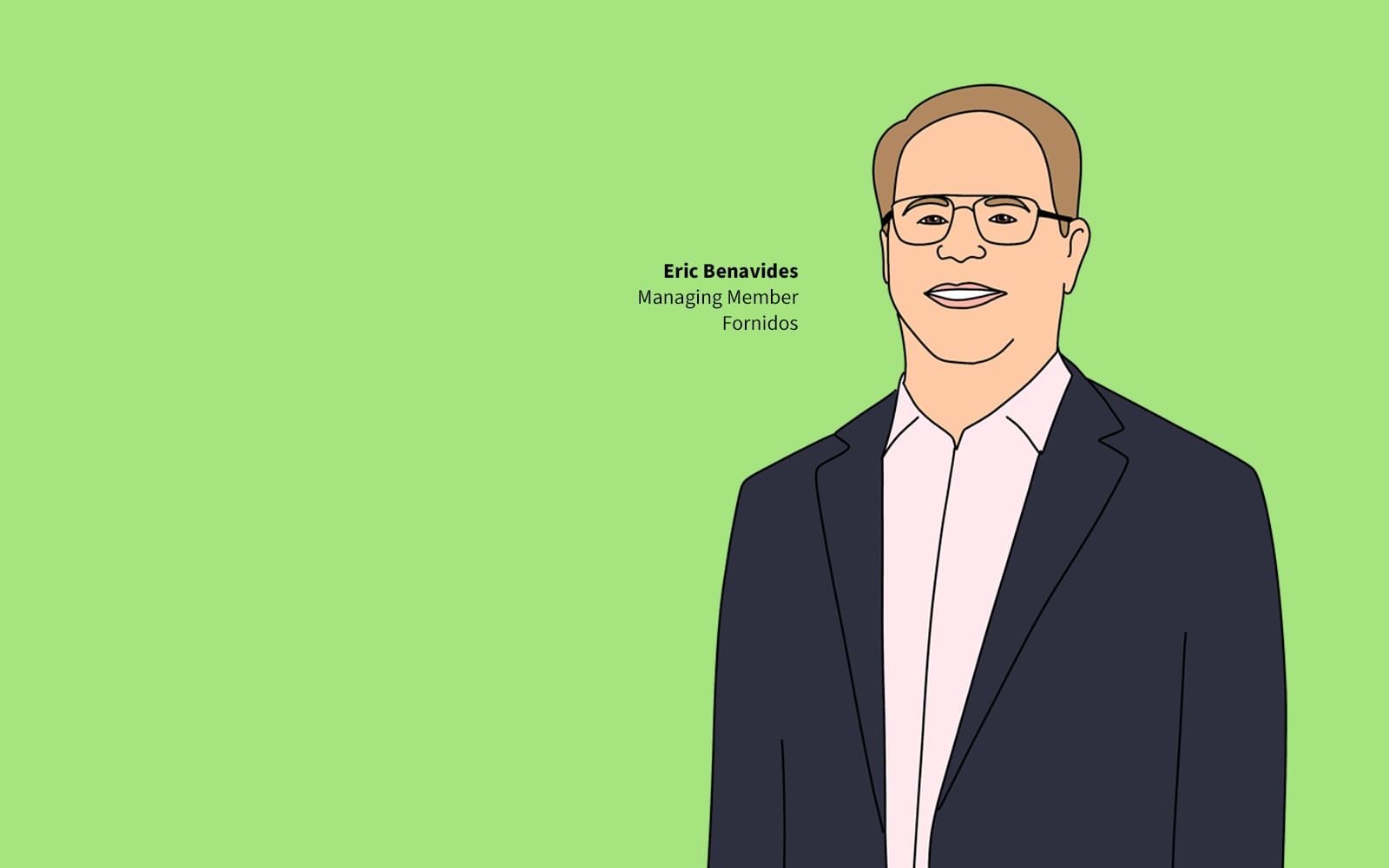
Many of us have a mental picture when we think of a housing innovator. Maybe it's a Silicon Valley engineer who cut their teeth in the automation-heavy factories of Tesla or Amazon, bringing a software-first approach to a notoriously hands-on industry. That’s often the case. But not this time.
Eric Benavides has been working in residential construction for four decades. He’s built everything from high-end custom homes to multi-unit subdivisions to affordable workforce housing. He’s seen—and experienced—the obstacles that drive up costs and slow down production.
Now, with his startup, Fornidos, he’s developed a factory-built home construction system that could fundamentally change the way homes are built at scale.
Benavides' breakthrough is simple in concept but radical in execution: pre-certified, factory-built structural panels that don’t require modular or manufactured housing classification.
The Source Code
In other words, his system allows builders to construct homes as if they were stick-built—but with the speed and precision of a factory. His component-based approach is backed by an Evaluation Services Report (ESR) from the International Code Council (ICC), meaning his panels are pre-approved to meet national building codes, streamlining local permitting and inspections.
The ICC ESR is the secret weapon,” Benavides says. “Most builders don’t realize what an ESR really is. They know about UL certifications, about HUD codes, but an ESR means that the structural components of my system have already passed the toughest third-party engineering standards. That means cities don’t need to scrutinize my product like a modular or manufactured home—it’s already approved under the International Building Code (IBC). That changes the game.”
A Factory-Built System Without the Modular Label
The problem with modular homes has never been the concept; it’s been the execution. Traditional modular homes must be transported as complete structures, which limits customization, increases costs, and complicates logistics. Benavides’ approach eliminates those issues.
His Component Construction System (CCS) is designed for builders, not just factory manufacturers. The system produces floor, wall, and roof panels that arrive primed, insulated, and ready for rapid assembly on-site. The result? A home that can be framed in days rather than weeks while still allowing builders to handle mechanicals, finishes, and customization like they would with traditional stick-built construction.
If you’re a builder, this isn’t asking you to abandon what you know,” Benavides explains. “You’re still hiring the same subs. Your electricians are still doing the wiring. Your plumbers are still running their pipes. The difference is, instead of waiting on a framing crew to take weeks — if you can even find one—you’re putting the structure up in two days.”
That alone would be significant. But the real advantage comes in permitting. Unlike modular homes, which must be reviewed under separate state or federal guidelines, Benavides’ ICC-certified panels qualify under conventional residential codes. Thus, homes built with Fornidos panels can undergo the same approval process as any other new home.
Scaling for Speed and Affordability
Speed is the key to affordability, but the construction industry hasn’t caught up. Labor shortages and supply chain disruptions have driven up costs, making entry-level housing more difficult to produce profitably. Benavides argues that Fornidos offers a way to cut cycle times and scale up production without sacrificing quality.
We’re talking about a system that lets builders finish a home in 10 days. Not a skeleton, not a shell—the whole thing,” he says. “When you can do that, you don’t need a huge construction loan sitting out there for months. You don’t need to wait for inspections at every phase. That’s what kills builders—time and interest payments.”
Fornidos is also designed to be flexible in its manufacturing. Unlike conventional modular factories, which require massive capital investment, Benavides' system can be produced in smaller, lower-cost factory setups or even pop-up manufacturing sites for disaster relief and high-volume projects.
The whole idea is decentralization,” he says. “Instead of investing $100 million into one giant factory that only serves a regional market, you can set up a 30,000-square-foot production facility for a fraction of that cost and manufacture enough panels for a thousand homes a year.”
Financing and the Path Forward
Any housing innovation must fit into the financing ecosystem for it to succeed. Benavides' system skirts one of modular construction's biggest challenges: mortgage eligibility. Because Fornidos panels qualify under the standard IBC framework, homes built with the system qualify for conventional financing through Fannie Mae, Freddie Mac, and other lenders, removing a major barrier to adoption.
Manufactured housing still struggles with financing,” Benavides says. “Even modular homes are limited in their loan options. But when you build with Fornidos, it’s just a regular house in the eyes of the bank. That’s a huge advantage.”
Fornidos is expanding in an early stage, with its first licensed manufacturing partner, Global BuildTech, launching production in California. Benavides is also in discussions with several national builders who are looking for scalable solutions to the affordability crisis. However, he acknowledges that broad adoption will take time.
I’m looking for the right partners,” he says. “I don’t want to be a builder. I want to give builders the tools to move faster, to lower costs, to keep control of their process. I’m not saying this is the only way to do it—but it’s one of the only ways I’ve seen that actually works.”
The Road Ahead
The U.S. needs millions of new homes, but labor shortages, high costs, and regulatory slowdowns prevent supply from meeting demand. The industry’s biggest players—Lennar, DR Horton, and Clayton Homes—are all experimenting with offsite construction and industrialized building techniques. However, few solutions have cracked the code on speed, scalability, and permitting.
Benavides believes Fornidos is the missing piece of the puzzle: a construction technology that doesn’t require builders to overhaul their businesses, a factory-built system that still allows local subcontractors to do their work, and a solution that doesn’t get tied up in red tape.
Look, I’ve been doing this for 40 years,” Benavides says. “I’ve seen every problem a builder can run into. This isn’t about reinventing the wheel. It’s about finally making the damn thing roll faster.”
MORE IN Technology
Lennar Taps Into Geothermal To Power New Colorado Homes
A major homebuilder's bet on geothermal heating and cooling for over 1,500 new Colorado homes could pave the way for mainstream adoption as buyers increasingly seek sustainable, energy-saving features.
AI Crushes Missing-Middle Time And Cost Curves Toward Affordability
Developing multifamily rental and for-sale properties takes time — sometimes years -- depending on a labyrinth of zoning rules and the whims of local jurisdictions.
Brandon Elliott’s Next Big Thing: An Uber-Style Building Trades Platform
After selling Elliott Homes to Meritage, the Gulfport, Miss.-based entrepreneur sets his sights on transforming trades with a logistics-tech startup that aims to make construction faster, smarter, and more affordable—starting with siding.